7 helpful tips for industrial machine maintenance
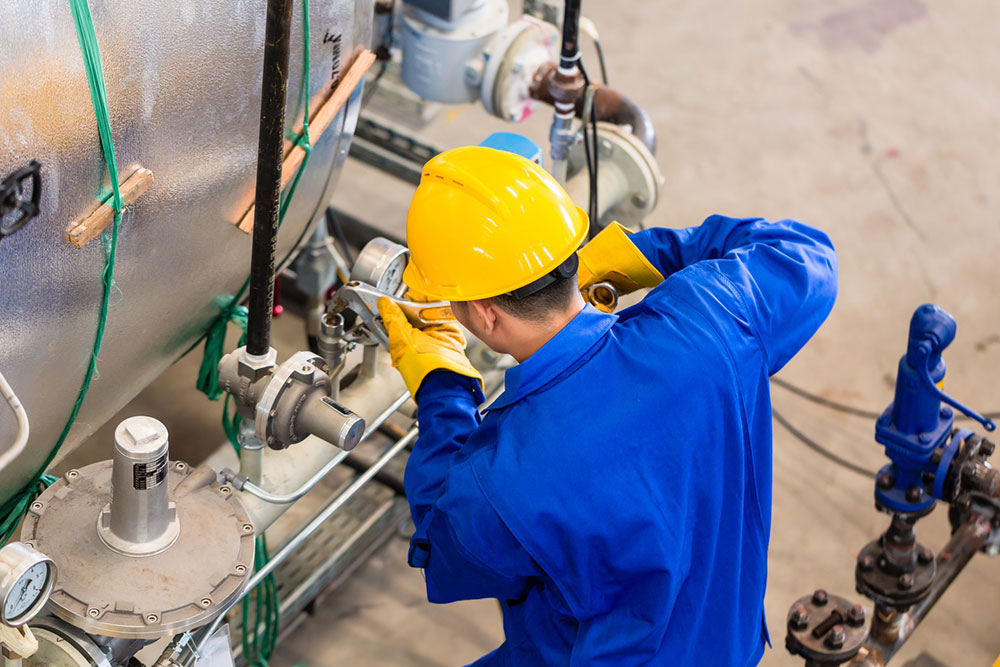
Industrial machine maintenance is a critical aspect of safety protocol that helps to prevent workplace accidents. These checks and balances are essential and should be performed regularly, as they can detect any irregularities early on, making it easier to fix problems without causing significant damage. Managers overseeing projects or sites in a factory should keep an eye out for these industrial machine maintenance tips to ensure the safety of everyone within the compound and beyond.
Clean the machinery regularly
It is very common for dirt and debris to accumulate on industrial machinery, which leads to the wear and tear of the machine. Corrosion, rust, and retaining rings are complications that arise with regular use. This can lead to malfunctioning of the machine, causing safety issues. So regular cleaning is of utmost importance when it comes to these machines. Reach all the joints and smaller sections of the machine, which are often overlooked. Another vital step of cleaning is making sure to apply a rust-preventing coat on all the exposed metal areas. Also, for some parts of the machine, it is advised to speak to a professional who knows the best cleaning methods.
Inspect the safety features regularly
Each machine has various safety features embedded in them. These include features like warning signs, emergency shut off, guard rails, alarm systems, and so on. Being mindful of these safety features can help avert any accidents at the workplace. Always check if these features are working properly, and if there is any issue, it needs to be addressed immediately. Do not ignore any of these warning signs. A regular inspection also involves looking at every small part of the machine. Any small noggin which is loose or placed improperly has the potential to create an accident. The best way to avoid this kind of risk is to check the machinery regularly and make notes.
Perform calibration checks
Depending on the type of work, machines require a calibration check every few weeks or months. The best way to understand this is to speak to the manufacturer and follow the user manual they suggest, along with the calibration check process and timeline they recommend. It is essential to have a professional technician assigned to these machines who can provide regular service to ensure that wear and tear does not affect the machine’s full potential. In case of any replacements or repairs required, the technician can easily take care of them in time and prevent any mishaps.
Inspect machines that have been out of use
There may be machines that have not been used for some time and are being used now to help with the workload. Before these machines are used for any kind of work, a professional checkup is needed to understand their functionality and effective working conditions. This way, if there are any issues, they can be addressed at the beginning of the project, avoiding delays later on. Recalibrating the machine might be needed if the task requires it, so always be prepared for all the scenarios.
Check lubrication
This may seem like a small step in the cleaning process, but proper lubrication can save the factory several thousands of dollars worth of time. When there is friction in the machine, it starts to break down. This temporary breakdown can cost the factory a lot of money due to delays in production and delivery. Therefore, one must always check the lubrication in high-speed spindles, motors, and such before starting a project involving the machine. Also, using the right kind of lubrication for different parts and machines plays a significant role in keeping them functioning well.
Maintain a log
This is a record of the machine’s usage, its last maintenance, and other important details. When monitoring a machine’s performance, these data points are beneficial in understanding its functionality and productivity. The log diary should also include any issues that were experienced during the last use of the machine, if any. This warns the person using the machine to be careful and vigilant of possible failures. Also, it is essential to include the date and name of the person using the machine, as they may have valuable insights that will aid in the maintenance process.
Resolve issues immediately
It is important to promptly address any issues that arise with the functioning of machines, particularly in industrial environments. Such problems can lead to other complications and compromise the safety of the people working there. Therefore, it is imperative to adhere to the established protocols when it comes to maintenance and repairs. Even if the cost of repairing the machine is high, it is important to consider the consequences of allowing an unserviced machine to operate in a facility where people are working. Safety protocol must always take priority over any other capital gains, and it is essential to be mindful of this fact.
One should speak to the manufacturer and get a team of professionals ready to tackle any such maintenance issue in the factory. They are well-versed in the process and can easily assist in navigating the problem. If there are any risks involved, always keep the workers informed for their safety and take the necessary measures to continue the maintenance protocol. Moreover, a monthly meeting can be held to discuss any machine issues that the team working on them is facing.