9 common mistakes to avoid with prefabricated metal building kits
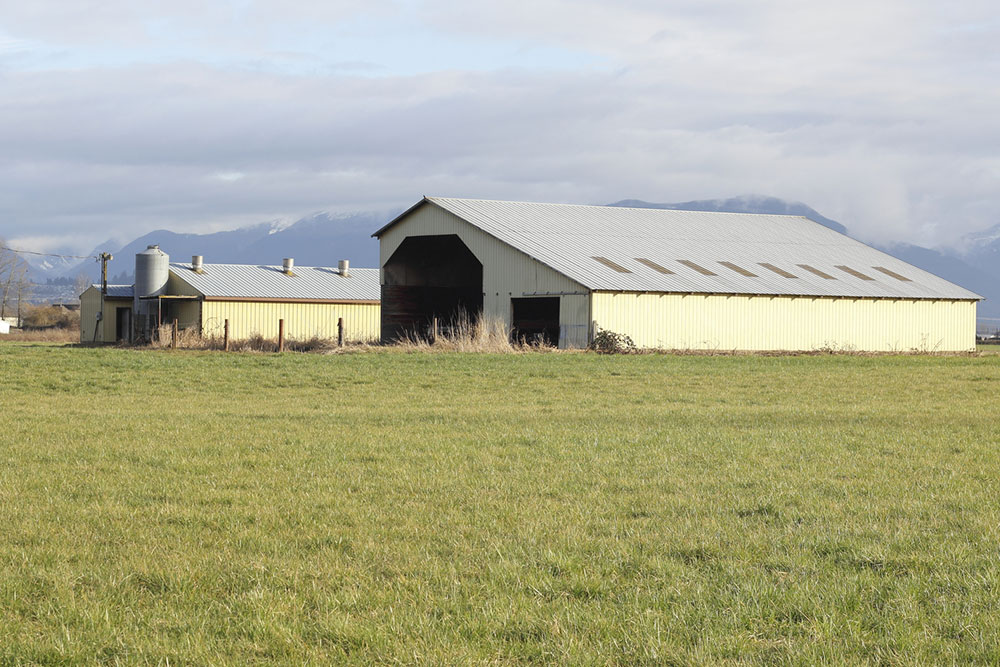
Construction projects, including prefabricated metal building kits, are quite challenging, given that one needs to factor in multiple variables throughout the project. One should err on the side of caution, as even the most minor mistakes can require demolishing and reconstructing various parts of structures, leading to losses of thousands of dollars. Therefore, those who take up a prefabricated metal building project should know how to avoid these common mistakes.
1. Overlooking local building codes
Every building project must adhere to building codes set by the local governing bodies. These rules and regulations are in place based on multiple factors. Therefore, overlooking the code and laying down a prefabricated metal building could lead to disasters in the future. For instance, one might disrupt electrical wiring and such throughout the building process, affecting the entire neighborhood. Additionally, failing to follow the rules could lead to the builder incurring heavy fines and facing legal action.
2. Picking the wrong building size
A project head must consider the land they have to work with accurately and the amount of room needed inside the building. A smaller building might require one to expand sooner than they anticipated. Of course, it is easier to expand a metal building than a traditional building. However, taking it up sooner than expected could lead to unforeseen expenses. On the contrary, one should also avoid designing a large building if it isn’t required. This may amount to higher expenses where materials and labor are concerned.
3. Failing to follow directives
A metal building kit usually includes detailed assembly instructions that should be followed carefully. The instructions might be a little lengthy, but they are typically straightforward, making setting up the prefabricated metal structure easy. However, ignoring some or all of the instructions could go sideways quickly. Winging the setup could compromise the integrity of the building, requiring expensive repairs and jeopardizing the safety of the individuals working on the building project. One should ensure they always follow the instructions given by the manufacturer.
4. Neglecting foundation strength
A metal-building kit requires a Stanley foundation to sit on. Therefore, failing to set a foundation or creating a poor-quality option might result in building shifts, structural damage, and even collapse. If this happens, one might have to make repairs that include exorbitant costs shortly. Apart from costs, a poor structure also compromises the safety of individuals in and around the building. When dealing with a prefabricated metal building kit, one must consider the type of foundation best suited for the needs of the building. A few types include reinforced masonry, concrete, or a combination of different materials.
5. Purchasing from an unreliable manufacturer
Several manufacturers offer prefabricated metal building kits. A few might offer a structure for prices that is too good to be true. One should remember that cheaper building materials are typically made of inferior materials, meaning they may suffer from wear and tear much faster. In this case, one might need to pay to repair or replace these materials more frequently, which may carry added costs. One should look for manufacturers that offer good-quality materials at a fair price.
6. Not budgeting for the whole kit
One should decide on a budget for the prefabricated steel building kit. However, one must remember that the kit does not include other items like doors, skylights, and windows. Therefore, overlooking this aspect may result in higher and unexpected costs when one includes them later on. One should ensure they consider all of the things required along with the building kit so that they can budget for it in advance. Additionally, getting all the supplies at once will avoid double transportation costs.
7. Picking the wrong metal type
A common mistake made while buying the kit is picking the wrong metal type. One should be mindful of the various types, such as aluminum, zinc, and steel. Each option has its own unique properties and advantages. For instance, an aluminum frame is lightweight and corrosion-resistant. On the other hand, steel is more durable, strong, and easy to recycle. When selecting the type of metal for the building kit, one should consider the local climate and weather conditions.
8. Going with incorrect insulation
One of the most common mistakes when buying a metal building kit is picking the incorrect insulation. Prefabricated metal kits differ from concrete or wood buildings and may require spray-on insulation. The spray works well, sticking easily to the metal while taking up minimal space. Manufacturers may also offer custom-designed insulation for the interior walls of metal structures. One should also consider the type of ventilation added to the building, as it could help keep it cool and dry.
9. Failing to speak to an expert
Many individuals take on projects without consultation, including prefabricated metal building kits. However, those inexperienced in the field may goof up with some installation steps, which could cause safety concerns. Whether dealing with elements like the kit, foundation, windows, and doors, one should always consult a professional who is well-versed in handling such installations. The professional may also recommend what one may or may not require throughout the project, which could help balance expenses.